Published on
30.06.2023
Reet Aus is a designer, researcher, activist, lecturer, visionary. Reet Aus holds a PhD from the Estonian Academy of Arts, where she is also a senior researcher and one of the initiators of the Sustainable Design and Materials Lab DiMA. Her research focuses on the industrial upcycling and recycling of materials in the fashion industry. As a pioneer in the field of industrial upcycling for fashion, Reet Aus has developed the UPMADE® certification.
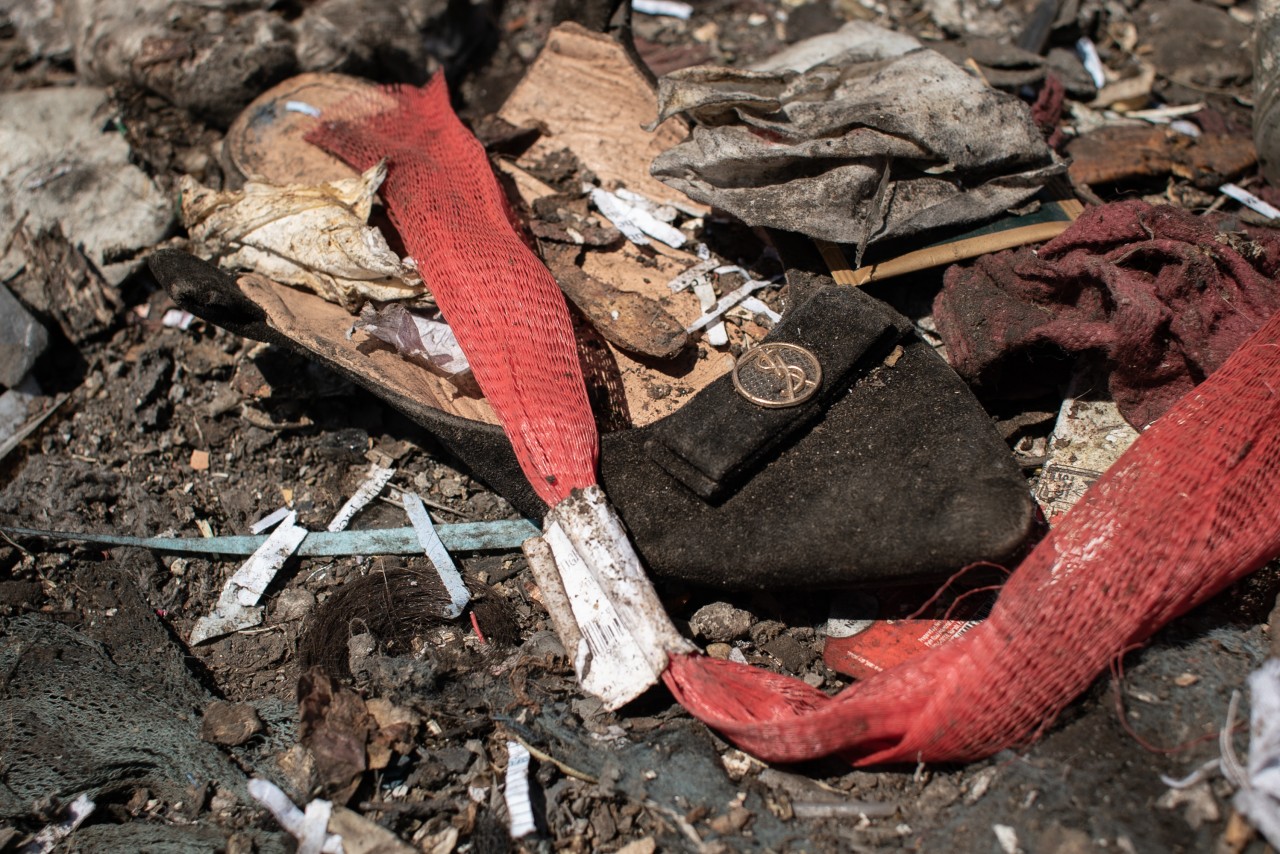
Surrounded by the acrid smell of garbage, I stand in the middle of the Dandora landfill in autumn 2021 and gaze at a superb suede shoe by Yves Saint Laurent under the burning sun. How did it get here? I take a look at the seemingly endless, as if self-created, landfill, and realise – here lies the one possible finale for haute couture design. In our consumption-oriented culture, it is still shocking to see that our beloved items become trash. We are unaware of where the things we no longer need end up. As a New York lawyer once said when I asked him if he knew where his hometown trash went: “Out of town on the train.” Indeed, we pick up things from store shelves, and when we no longer need them, they disappear from our lives. But how do they wind up on store shelves and where do they go afterwards? Why don’t we think about it?
It is quite unexpected to meet what we in our consumer society consider quality design in Sub-Saharan Africa, in a Nairobi dumpsite.
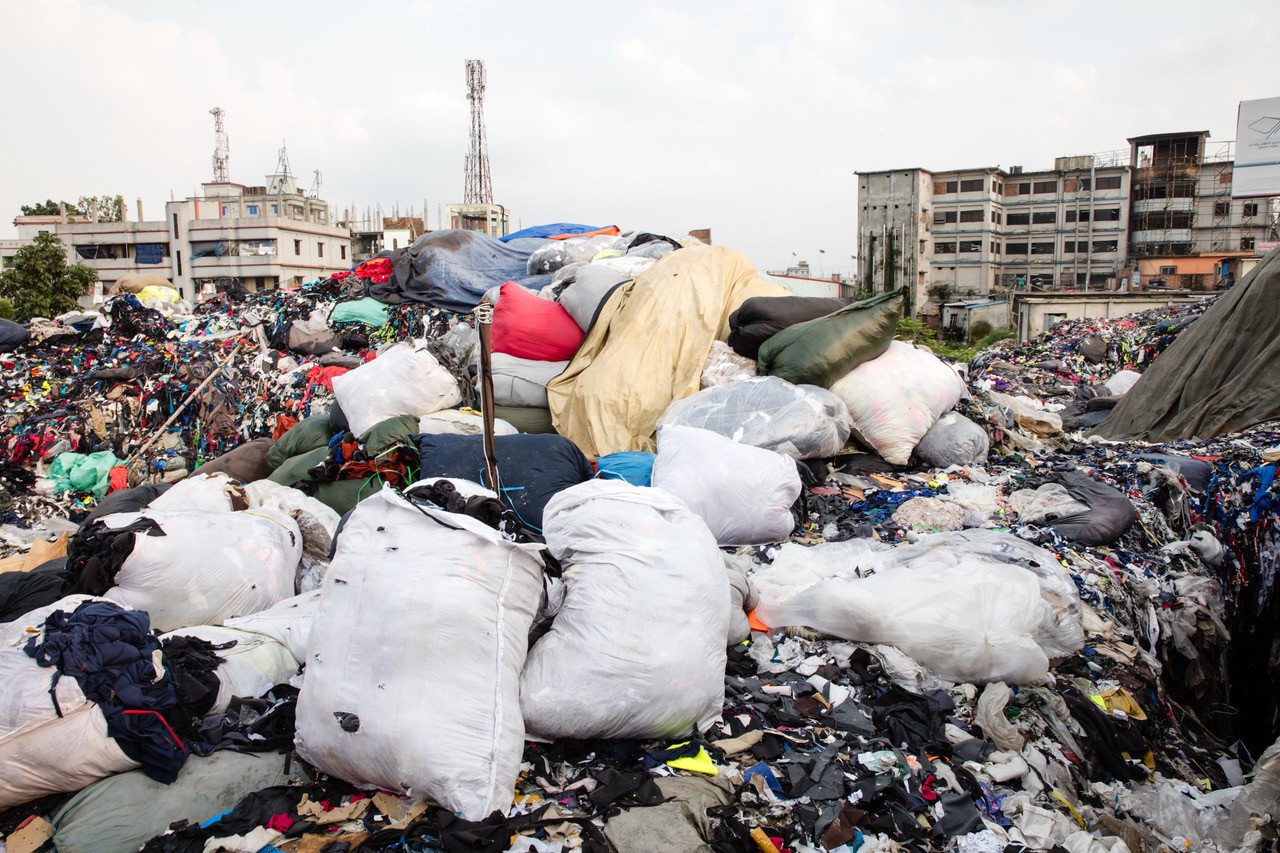
Industrial area in Gazipur, Bangladesh
I have visited this place around 20 times within the last ten years. During this period, almost nothing has changed – huge factories and endless mountains of textile waste towering all around. Children and dogs climb on top of these piles, triumphantly conquering them. Textile waste goes mouldy and produces aromas that you cannot easily forget. In a few days, your own sweat starts to smell similar. It’s code red for air pollution, the noise is deafening. The coloured wastewater flows directly from the factory into the Buriganga river.
Only one factory among all the factories in Gazipur has engaged in industrial upcycling. This means that a part of the excess materials finds its way back into the production. Unfortunately, it really is only a part and only one factory. The global brands that manufacture in Gazipur and who own these excess materials are not lifting a finger to improve the situation. As the brands are the ones who have the sales channels and the money – meaning also the decision-making power – the factories in Bangladesh can only become more sustainable and circular if they engage in close collaboration with those who commission from them. The brands are not interested in that, however. Depending on the size of the factory, the textile waste generated in the clothing industry is 25–40% of the total fabric used. If desired, it would be possible to reuse 50% of this material using the upcycling method to make new clothes, for certain types of waste, or to even reuse up to 80
In this video, you can see how the arrow T-shirt conceived by my brand is made using the industrial upcycling method in a factory called Beximco in Bangladesh. This is one example of how excess materials from factories could be used to manufacture new products. Making a shirt from existing material helps save water and reduce the energy required for production, while limiting waste generation. The arrow shirt has been in production for nine years and continues to be the brand’s best-selling product. One T-shirt saves 99% of water and 86% of CO₂ compared to a T-shirt made of new fabric.
In order to change the current processes, it is necessary to shed light on the entire life cycle of an individual product. It is important not only to know where we produce something, but also how we do it. Is the product designed in a way that it avoids waste? There is quite a big difference if the efficiency of the product’s cut pattern is 45% or 94%, and this in turn is a matter of design. How much fabric is left over in production and how is this recycled? What recycling techniques are used and what do the supply chains of large corporations look like? How can we avoid the environmental damage induced by manufacturing and waste generation? Would it be possible to reach such a collaboration between the brand and the manufacturer that would provide solutions to problems, instead of aggravating them?
Bangladesh, where the locals wear mostly culturally traditional clothing (sari, kurta or lungi), exported garments worth 42.613 billion US dollars in 2022. This made Bangladesh the second largest apparel exporter in the world after China (Export Promotion
Gikomba Market, Nairobi
As in other welfare states, Estonia sends their textile waste to Africa through organisations that collect used clothing. In the port of Mombassa, Kenya, ships dock with containers full of carefully packed textile waste – those slightly worn out clothes that the Europeans have discarded. The textile bales go to Nairobi, to presumably the world’s largest second-hand market, Gikomba. Part of the goods are bought by small entrepreneurs who resell them on their counters all over Nairobi. However, a large part of the textile bales remain in Gikomba because at the end of the day it is garbage that no one needs. Our old t-shirts and jeans, that once so convincingly described our identity and values, and that in the best case scenario now reflect our personal history, find their way from the Nairobi market to the local river, fields or the Dandora dumpsite. Flooding the local market with useless textile waste has pushed Kenya’s textile industry, traditional crafts and cultural sustainability to the brink of extinction.
Clearly, we have reached a point where Western societies must start to admit that the products we consume have a devastating effect on the environment, culture and people, and this applies to all stages of the product’s life cycle, while the damage increases the further we move from home. However, distance does not take away our responsibility, on the contrary – the producing country manufactures these clothes, while exploiting the labour force and environment, especially for us. We come in contact with the product only in its consumption phase, through massive sales campaigns, discounts, varying fashion trends and Instagram stories, through a rampant celebration of consumption. It starts with the magical appearance of the product on the store shelf and lasts until the minute when we no longer desire it. From there on, a journey to the unknown begins. The product finds its way back to where it started from. Be it the Bangladesh factory as the starting point or the Dandora landfill as the end. For us, it is all a big somewhere else. The entire life cycle of a fashion product can be summed up with the words of my good friend – from the unheard-of to the unrenowned.
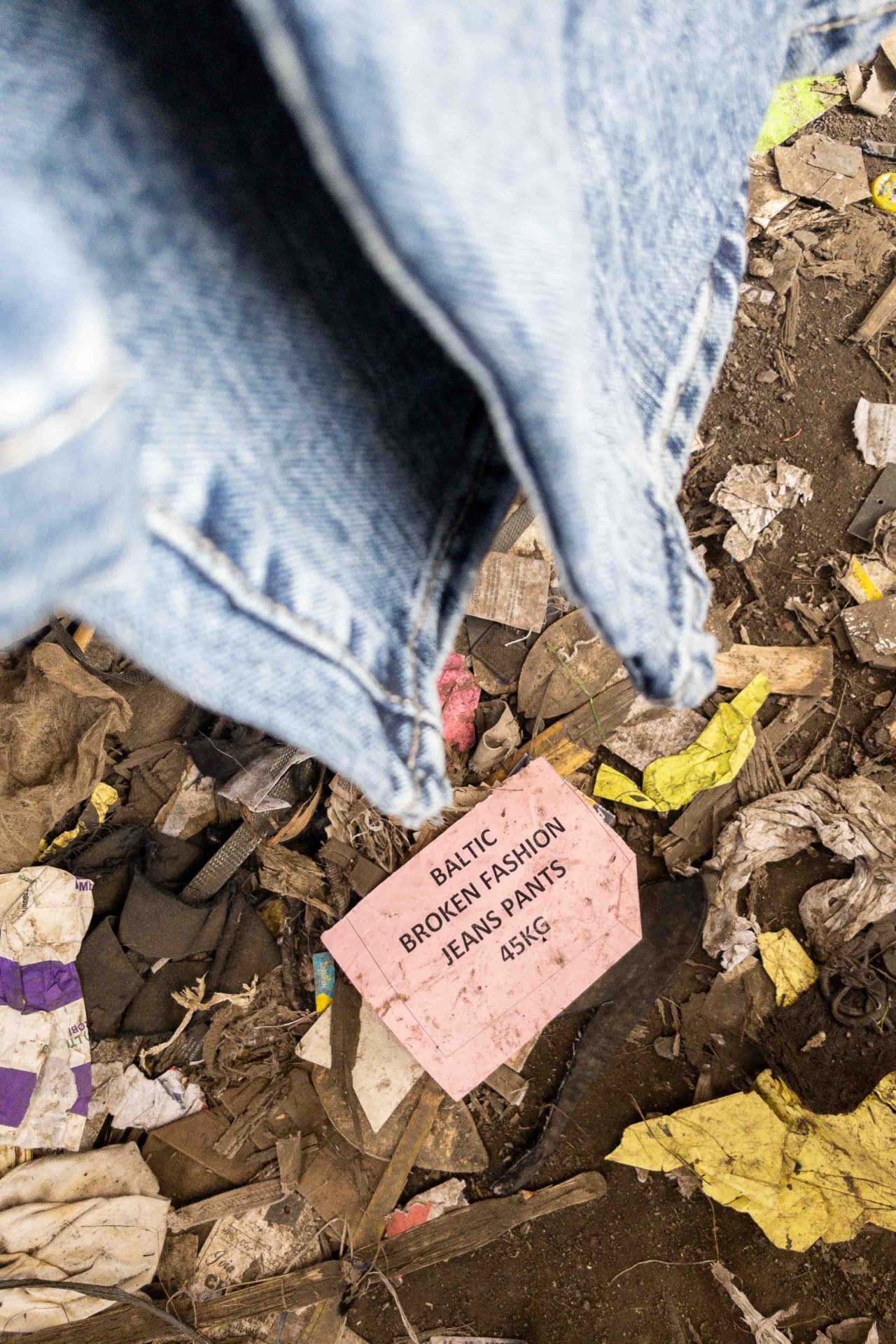
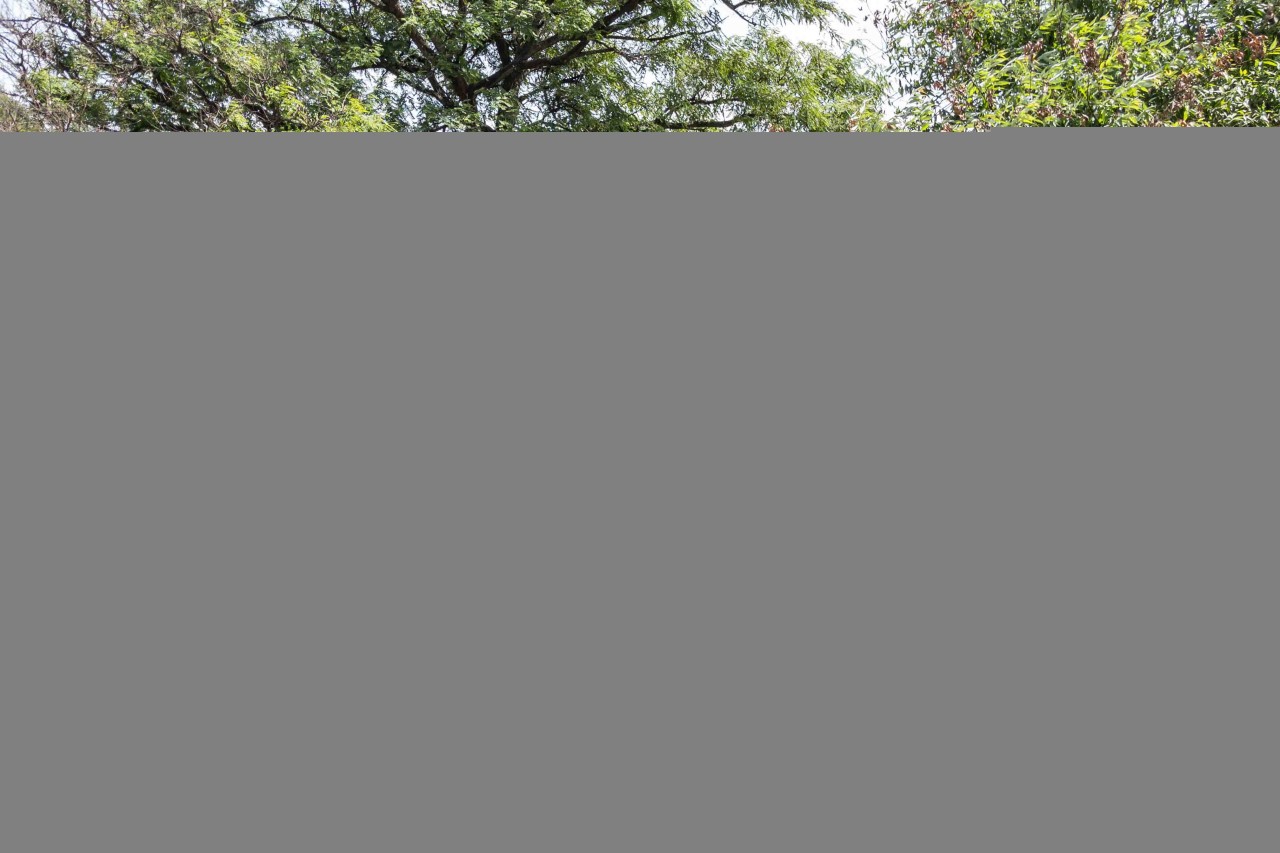
Is an item that ended up in the trash a reproach to the designer? Proof of the designer’s downfall? Standing on top of the Dandora landfill, which had recently swallowed an entire large excavator, I am struck by the sad realisation that we are very skillful at producing garbage. We produce things that have no value. For some reason, however, we refuse to admit that it is not only a problem concerning waste, but an inability to create and market long-lasting, high-quality manufactured products according to circular principles. For decades, we have educated designers who create aesthetic value, but not enough of them are aware of circular design or the life cycle of the product. And how could they know any better considering that in their studies they have never been taught how the large-scale industries work or where this unrenowned Kenya is where we send our used items? It is necessary to make a connection between the endpoints of the product’s life cycle in order to create a big picture. Both the factories in Bangladesh and the landfills in Kenya are separated from our European welfare state by just a few hours on a plane, yet sometimes it seems they are situated on another planet.
Who should take responsibility for the current situation, responsibility for the people of Nairobi who find before them not store shelves that are overstocked, but landfills full of items, created by the same highly educated designers? Who should be held responsible for the environmental damage, social problems, loss of heritage and climate change? Before ending up in the landfill, every item has gone through the design, product development, sampling and manufacturing phases, and then found its way through the purchase and sale transaction to the user who at some point discards it. It’s no secret that the global industry goes together with a multitude of problems that we generally ignore. The opacity of linear supply chains, the vast environmental damage induced by manufacturing, the underpayment of workers and the huge profits of large corporations only benefit from our indifference.
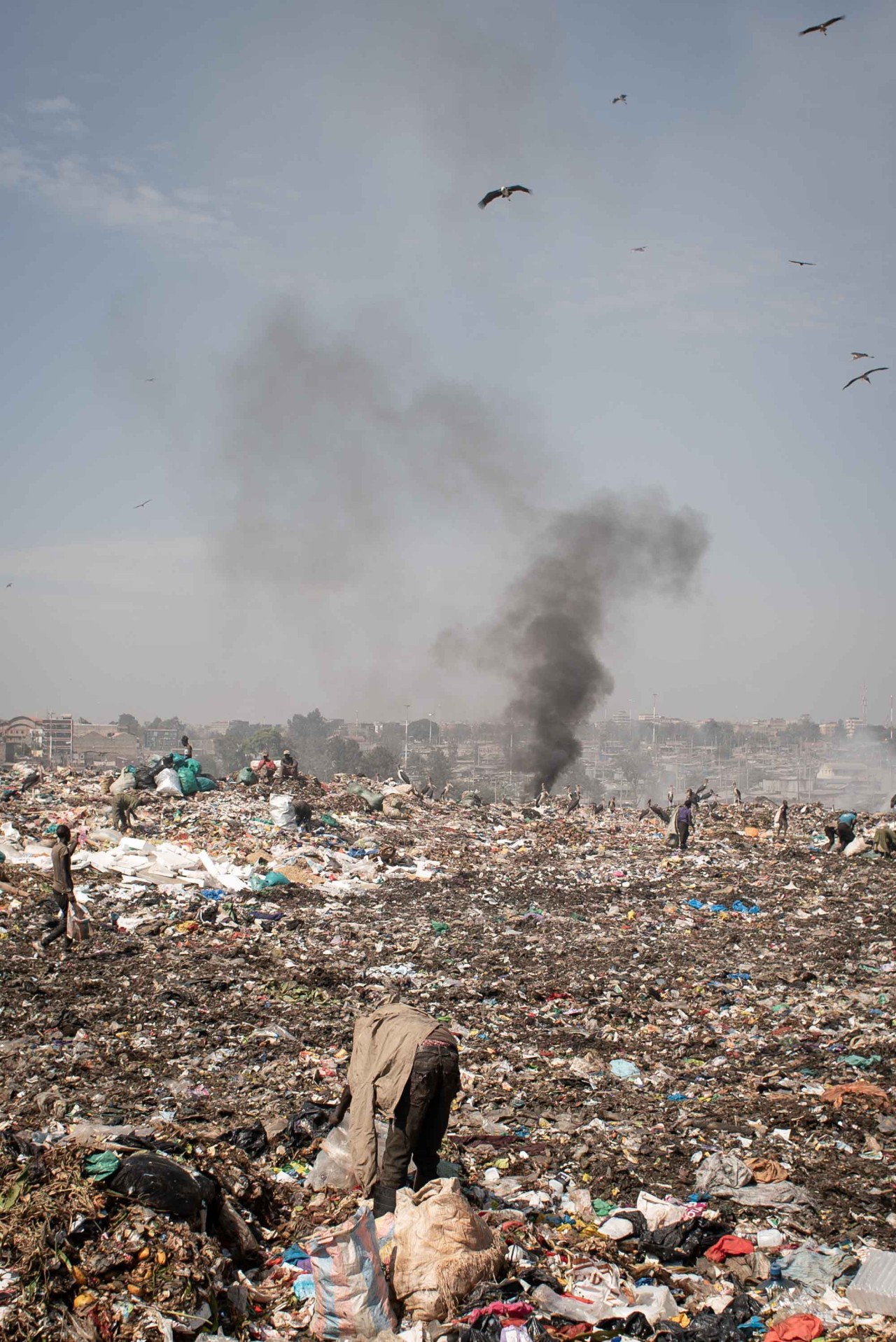
Circling back to the beginning
We must come to terms with the fact that the fashion industry is faced with several difficult challenges. There seem to be no solutions, and the globally constructed production chain is so puzzling that no light appears to shine from any end. Yet, when you look at the problem from the designer’s point of view and on a product basis, taking the entire product life cycle apart, it turns out there are solutions at every stage. A cleverly designed item with a mapped out future and a transparent past helps us avoid almost all of the problems mentioned above. This creates a chain where waste is used as input material, making a closed circular system, where the products are designed, manufactured and used in a way that allows them to enter the circulation after use because they have been designed like this! The surplus generated at each stage of the life cycle is used as input material for creating something new either within or outside the same industry. Looking at the life cycle of the product, we can see that the designer is able to influence the entire process of the product based on the selection of the material, efficiency of the cut pattern, production technology etc. For example, if the designer decides to choose an upcycling method, the production of new material is immediately dropped; thus, making the environmental impact of the product many times smaller, compared to a product made from primary material. This also reduces the carbon footprint and water consumption. In the case of garments designed and produced in this way, we are talking about high-quality timeless design, products that will not go out of fashion in one season.
References
- Aus, Reet et al., ‘Designing for circular fashion: integrating upcycling into conventional garment manufacturing processes’, Fashion and Textiles, 8(34), (2021). <https://doi.org/10.1186/s40691-021-00262-9>
- <http://www.epb.gov.bd/>.
- <https://www.eea.europa.eu/en>.